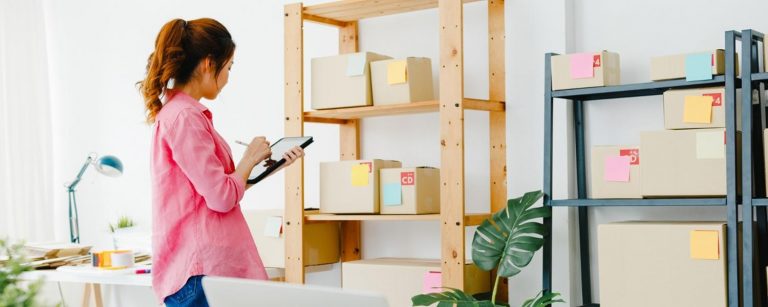
Businesses across industries depend on reliable tracking and maintenance of their physical assets to ensure operational continuity. Implementing robust construction equipment management software can dramatically improve efficiency and reduce costs associated with asset oversight. This article explores key considerations for selecting the most appropriate solutions for your organisation’s specific requirements.
Understanding Equipment Tracking Requirements
Equipment tracking tools serve as the foundation for comprehensive asset oversight. These systems provide organisations with capabilities including:
- Real-time location monitoring of critical assets
- Assignment tracking for responsibility management
- Utilisation analysis for capacity planning
- Depreciation calculations for financial reporting
- Warranty and service contract management
The effectiveness of equipment tracking tools depends largely on their alignment with specific organisational workflows. Manufacturing firms typically require detailed component-level tracking, while service organisations might focus more on availability and customer allocation.
UK construction companies report significant improvements in project delivery timelines after implementing structured tracking solutions. By maintaining accurate records of equipment location and status, project managers can schedule work confidently without the delays previously caused by equipment availability uncertainty.
Healthcare organisations face unique challenges requiring specialised tracking approaches. Medical equipment must be monitored not only for location but also for calibration status, cleaning verification, and compliance with regulatory standards. Effective tracking systems accommodate these requirements while integrating with patient management systems.
Core Features of Resource Management Solutions
Resource management solutions extend beyond basic tracking to encompass broader operational considerations. Key functionality includes:
- Resource allocation and scheduling
- Capacity planning and forecasting
- Utilisation analytics and optimisation
- Integration with financial systems
- Customisable reporting and dashboards
“Our implementation of comprehensive resource management solutions reduced equipment downtime by 23% while improving capital utilisation rates,” notes the Operations Director at a prominent British manufacturing firm. “We gained visibility into usage patterns that allowed us to optimise our equipment fleet size.”
For organisations with mobile workforces, resource management becomes particularly critical. Field service operations depend on ensuring technicians have appropriate equipment available when needed. Advanced systems incorporate route optimisation and job scheduling alongside equipment tracking to maximise workforce productivity.
Educational institutions benefit substantially from structured resource management. Universities and colleges manage extensive equipment portfolios ranging from laboratory instruments to audiovisual systems. Tracking these assets across multiple buildings and departments represents a significant challenge that purpose-built solutions can address effectively.
Benefits of Maintenance Management Systems
Maintenance management systems play a crucial role in extending equipment lifespan and preventing costly downtime. These platforms enable organisations to:
- Schedule preventive maintenance activities
- Track maintenance history and costs
- Manage spare parts inventory
- Document standard maintenance procedures
- Generate work orders and assign technicians
Effective maintenance management systems shift organisations from reactive to proactive maintenance strategies. This approach reduces emergency repair costs while extending equipment lifespan through consistent care.
The financial impact of structured maintenance management can be substantial. A UK-based logistics company documented a 31% reduction in fleet maintenance costs after implementing a comprehensive system. “Beyond direct repair savings, we significantly reduced downtime-related losses that previously impacted customer satisfaction,” explained their Fleet Manager.
Predictive maintenance capabilities represent an advanced feature of modern systems. By analysing performance data, these systems can identify potential failures before they occur. This capability is particularly valuable for organisations operating critical equipment where failures would result in substantial operational disruption.
Compliance requirements add another dimension to maintenance management challenges. Industries such as food processing, pharmaceuticals, and aviation must maintain detailed maintenance records to satisfy regulatory obligations. Purpose-built systems ensure this documentation remains complete and readily available for inspection.
Integration Considerations for Comprehensive Management
While individual tools address specific needs, maximum value comes from integration across platforms. Organisations should evaluate how potential solutions will interact with:
- Enterprise resource planning (ERP) systems
- Accounting and financial platforms
- Purchasing and procurement systems
- Human resources and scheduling tools
- Customer relationship management platforms
Integration challenges often present the greatest hurdle to successful implementation. Legacy systems may lack modern API capabilities, requiring custom development work to achieve data synchronisation. Organisations should carefully assess integration requirements before committing to specific solutions.
Data standardisation represents another critical integration consideration. Different departments often use varying terminology and classification schemes for equipment. Successful implementations establish consistent naming conventions and categorisation frameworks to enable meaningful cross-functional reporting.
For multinational organisations, integration must accommodate regional variations in regulatory requirements, accounting standards, and operational practices. Systems should support multiple currencies, languages, and compliance frameworks while still providing consolidated reporting capabilities.
Cost-Benefit Analysis of Management Solutions
Investment decisions should consider both direct and indirect benefits, including:
Direct Financial Benefits
- Reduced emergency repair costs
- Extended equipment lifespan
- Lower capital requirements through improved utilisation
- Decreased administrative overhead
- Optimised inventory carrying costs
Operational Improvements
- Enhanced equipment availability
- Improved workforce productivity
- Better capital planning accuracy
- Reduced project delays
- More reliable service delivery
A comprehensive Yorkshire manufacturing firm conducted detailed analysis of its implementation outcomes, documenting a 187% return on investment over three years. “The system paid for itself within eight months through direct cost savings alone,” reported their Financial Controller. “When factoring in productivity improvements and reduced capital requirements, the benefits were substantially greater.”
The implementation approach significantly impacts the cost-benefit equation. Cloud-based solutions typically require lower initial investment but higher ongoing subscription costs. On-premises deployments involve larger upfront expenditure but may prove more economical for very large installations over extended periods.
Data migration costs deserve particular attention during budgeting. Organisations with extensive existing equipment records may face significant effort transferring this information to new systems. Automated migration tools can reduce this burden, but customisation is often required to accommodate unique data structures.
Security and Compliance Requirements
Equipment management platforms often contain sensitive information requiring appropriate protection. Security considerations include:
- Access control and permission management
- Data encryption standards
- Audit trail functionality
- Compliance with industry regulations
- Disaster recovery capabilities
The UK’s General Data Protection Regulation (GDPR) impacts equipment management when systems store information about equipment operators or maintenance personnel. Organisations must ensure their chosen solutions provide appropriate privacy protections and data subject access capabilities.
For regulated industries, equipment management systems must support specific compliance requirements. Healthcare organisations must demonstrate equipment safety and calibration records. Manufacturing firms must document equipment qualification and validation. Solutions should provide appropriate documentation capabilities aligned with relevant regulatory frameworks.
Implementation Best Practices
Successful implementations typically follow these principles:
- Begin with process assessment: Document current workflows and identify improvement opportunities before selecting technology.
- Establish clear success metrics: Define specific, measurable objectives for the implementation to evaluate outcomes.
- Conduct thorough data cleansing: Clean and standardise equipment records before migration to prevent perpetuating existing problems.
- Implement incrementally: Start with core functionality in a limited area before expanding to broader deployment.
- Invest in user training: Allocate sufficient resources to ensure staff can utilise system capabilities effectively.
Organisations achieving the greatest success typically establish dedicated system administrators with responsibility for ongoing optimisation and support. These individuals serve as internal experts who can assist colleagues while maintaining system configuration as business requirements evolve.
Change management deserves particular attention during implementation. Technical and maintenance staff often have established work patterns that new systems will disrupt. Addressing concerns through clear communication about benefits and incorporating feedback during configuration significantly improves adoption rates.
Emerging Technologies in Equipment Management
The field continues to advance with technologies enhancing management capabilities:
- Internet of Things sensors for real-time monitoring
- Artificial intelligence for predictive maintenance
- Augmented reality for maintenance guidance
- Digital twins for simulation and planning
- Blockchain for secure maintenance verification
These technologies are progressively moving from experimental to mainstream adoption. Organisations should consider vendors’ innovation roadmaps when making selection decisions to ensure solutions will accommodate emerging capabilities as they mature.
Radio-frequency identification (RFID) technology has become particularly valuable for equipment tracking in complex environments. Passive RFID tags requiring no power source can be affixed to equipment and automatically detected when passing through strategic checkpoints. This capability dramatically improves tracking accuracy while reducing manual data entry requirements.
Mobile applications represent another significant advancement. Field personnel can access equipment information, report issues, and document maintenance activities through smartphones or tablets. These capabilities improve data quality by capturing information immediately rather than requiring delayed entry into office-based systems.
What to Do Next?
By implementing well-matched equipment tracking tools, resource management solutions, and maintenance management systems, organisations can achieve substantial operational improvements and financial benefits. The key lies in aligning technological capabilities with business requirements while ensuring appropriate attention to implementation practices and user adoption.
With the right solutions in place, organisations can transform equipment management from an administrative burden into a strategic advantage that supports operational excellence and financial performance. This structured approach ensures equipment remains an enabler of business success rather than a constraint on operational capability.