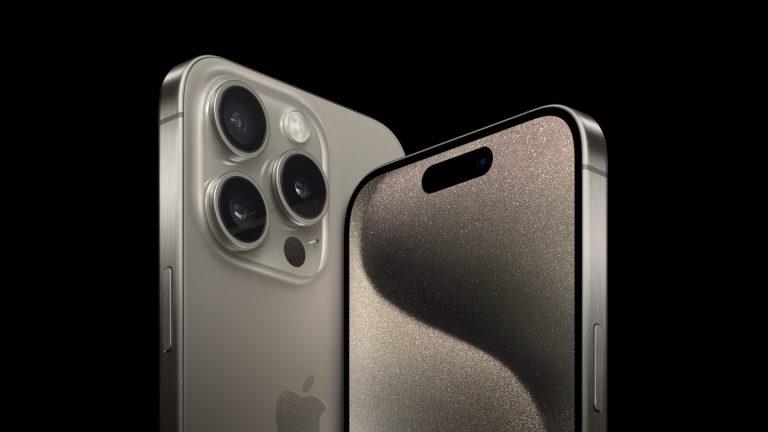
The Trump administration has long been fixated on the vision of bringing iPhone manufacturing back to American soil. This ambition, rooted in a broader “America First” economic agenda, aims to revitalize domestic manufacturing and reduce reliance on foreign production, particularly from China.
The idea has gained renewed momentum as the administration escalates its tariff war, imposing steep levies on imports from key manufacturing hubs like China, Vietnam, and India. President Donald Trump and his team, including White House press secretary Karoline Leavitt and U.S. Commerce Secretary Howard Lutnick, have repeatedly pointed to Apple’s recently announced $500 billion U.S. investment plan as evidence of confidence in this vision.
Leavitt has argued that products like the iPhone could realistically shift to U.S. manufacturing, stating, “If Apple didn’t think the United States could do it, they probably wouldn’t have put up that big chunk of change.”
Register for Tekedia Mini-MBA edition 18 (Sep 15 – Dec 6, 2025) today for early bird discounts. Do annual for access to Blucera.com.
Tekedia AI in Business Masterclass opens registrations.
Join Tekedia Capital Syndicate and co-invest in great global startups.
Register to become a better CEO or Director with Tekedia CEO & Director Program.
Lutnick has echoed this optimism, envisioning “millions and millions of human beings screwing in little screws to make iPhones” on American factory floors. However, this narrative collides with stark economic and logistical realities, rendering the dream of a Made-in-the-USA iPhone both impractical and prohibitively expensive in the near term. As tariffs intensify, Apple is instead scrambling to pivot its production to India, where labor and production costs, while not as low as China’s, offer a viable alternative to mitigate the financial fallout.
The Tariff War Boosting the U.S. Manufacturing Dream
The Trump administration’s tariff strategy, dubbed “reciprocal tariffs,” targets over 180 countries, with China facing a staggering 104% rate (including a pre-existing 20% levy), Vietnam at 46%, and India at a comparatively lower 26%. Effective as of midnight on April 9, 2025, these measures are designed to pressure companies like Apple to reshore manufacturing by making imported goods prohibitively expensive.
The administration sees the iPhone—a globally iconic product designed in California but assembled abroad—as a symbolic prize. Trump has explicitly tied Apple to this agenda, claiming during his tariff announcement that “they’re going to build their plants here.” This rhetoric aligns with his first-term efforts, where he successfully persuaded Apple to secure exemptions on certain products, and it reflects a belief that high tariffs will force a return to a bygone era of American industrial dominance.
The White House has leaned heavily on Apple’s $500 billion U.S. investment pledge, announced in February 2025, as proof of progress. This plan includes building an AI server factory in Texas and sourcing more parts from U.S. suppliers. Leavitt has seized on this, arguing that it demonstrates Apple’s faith in American labor, resources, and workforce capabilities.
Yet, analysts have tempered this enthusiasm, noting that the investment is “in line with what one might expect the company to be spending anyway,” rather than a radical shift toward mass iPhone production in the U.S. The tariff war has undeniably given this narrative a boost, but the practical challenges of making iPhones at home reveal a far more complex picture.
The Unaffordable Reality of U.S.-Made iPhones
Despite the administration’s fervor, producing iPhones in the United States faces insurmountable hurdles that would render them unaffordable for most consumers. Steve Jobs articulated this dilemma over a decade ago during meetings with then-President Barack Obama in 2010 and 2011, as detailed in Walter Isaacson’s biography. Jobs explained that Apple’s 700,000 factory workers in China were supported by 30,000 on-site engineers—a scale of skilled labor unavailable in the U.S.
“You can’t find that many in America to hire,” he told Obama.
Tim Cook reinforced this in 2017 at Fortune Magazine’s Global Forum, noting that China’s advantage lies not in cheap labor but in its “skill and the quantity of skill in one location.” He contrasted the U.S., where “you could have a meeting of tooling engineers, and I’m not sure we could fill the room,” with China, where “you could fill multiple football fields.”
The economics underscore this gap. Labor costs in the U.S. are significantly higher than in China or India, and the specialized workforce required for iPhone assembly doesn’t exist at the necessary scale domestically. Even if Apple attempted to train such a workforce, the process would take years and billions of dollars—far beyond the Trump administration’s timeline. Estimates of a fully U.S.-made iPhone’s cost have ranged wildly, with a 2018 Quora post suggesting $30,000 and a recent Reuters analysis pegging a tariff-impacted iPhone at $2,300.
While these figures are speculative, they highlight a consensus among economists and manufacturing experts: domestic production would drastically inflate prices. Rosenblatt Securities estimates that absorbing current tariffs without raising prices could cost Apple $39.5 billion annually, slashing operating profits by nearly 32%. Passing those costs to consumers could push the iPhone 16 base model from $799 to $1,142—a 43% hike—while the iPhone 16 Pro Max might hit $2,300, up from $1,599.
Beyond labor, the iPhone’s global supply chain complicates the picture. Components come from Japan, South Korea, Taiwan, and elsewhere, with rare earths mined across dozens of countries. Assembling these in the U.S. would require either importing them (subject to tariffs) or building entirely new domestic supply chains—an endeavor that could take decades.
Trump’s vision assumes every company restores simultaneously, but this would strain resources, exacerbate supply chain bottlenecks, and deepen the shortage of skilled workers. The result would be an iPhone so expensive it risks alienating Apple’s customer base, giving competitors like Samsung (facing a lower 25% tariff from South Korea) a market edge.
Apple’s Pivot to India Amid Tariff Pressure
Faced with these realities, Apple is not doubling down on U.S. production but rather accelerating a shift to India, where labor and production costs rank second only to China. The company has been diversifying its supply chain since 2017, initially assembling older iPhone models in India through partners like Foxconn, Tata Electronics, and Pegatron. By fiscal year 2024, India accounted for 14% of global iPhone production—about 25 million units—and exported nearly $9 billion worth to the U.S. With China’s 104% tariff dwarfing India’s 26%, the economic incentive to ramp up Indian output is clear.
Posts on X and reports from outlets like The Times of India indicate Apple is already acting, shipping five planes of iPhones from India to the U.S. in late March 2025 to beat the April 5 tariff deadline.
India offers a compelling alternative. Its labor costs are lower than the U.S., and its government has bolstered manufacturing with incentives like the Production Linked Incentive (PLI) scheme, disbursing nearly $1 billion to Apple’s partners since 2022. Foxconn plans to produce 25-30 million iPhones in India in 2025, doubling last year’s output, while Apple aims to hit 15-20% of total iPhone production by year-end, per Bernstein analysts.
However, India isn’t a perfect solution. Its manufacturing ecosystem lacks China’s scale and maturity, with a 6-7% higher production cost disability, according to industry estimates. Scaling to China’s level—where 90% of iPhones and 80% of iPads are assembled—could take years, and the 26% U.S. tariff still stings. But the 28-percentage-point tariff gap with China makes India the “least bad” option, as one industry official put it. Apple is also starting AirPods production in India this month, further signaling a long-term commitment.